Process for getting assignments for a Project order (POD)
Material
Process for getting assignments means getting material assignments from stock, procurement backlog or production work orders. Or if no available quantity, this process will create a purchasing need in the Purchase (PUR) application, or for manufacturing in the Production planner (PROPPLAN) application. The material will then be Pending in the Stock assignment (SAR) application.
You can start the process for getting assignments for either all Project order (POD) items, only one Project order (POD) item, or you can use the multiselect function. If you want to start the process for all Project order (POD) items at the same time, this is done from the main level on the Project order (POD). The process for only one Project order (POD) item or using the multiselect function is done at the Project order (POD) item level.
When the process for getting assignments is started, an internal Sales order (COA) for Material for project order will be created. Product, Remaining estimated quantity and Remaining estimated price from the Project order (POD) item will be copied to Sales order (COA) item. This Sales order (COA) item will behave like a regular Sales order (COA) item when it comes to logistics. It will get assignments from Goods reception (SSA), Purchase order (SPO), Purchase order response (SOA) or Production work order (PWO), or a purchasing or manufacturing need will be created for this item. It can be picked if there are goods already in stock. There will always be a one-to-one relationship between this Sales order (COA) item and the Project order (POD) item.
If the need for a material is changed after the internal Sales order (COA) has been created, the assigned quantity can be changed by update of remaining estimated quantity, either by a positive or negative number. Use then the context menu item Update quantities for material assignments. This will cause the Sales order (COA) item to be forwarded to a new Sales order (COA), and the number will be reduced or increased according to Remaining estimated quantity. In any case, the number can never be reduced to a lower quantity than what has already been picked.
Start the process for getting assignments
If the Project order (POD) item(s) is not already registered, the item(s) will have Status 1, you must use the Register project order option in the context menu. The Project order (POD) item will go from Status 1 to Status 4.
Start the process for getting assignments by selecting Project order (POD) item(s). Select the item(s) by clicking on the status symbol on the item line. It is possible to start the process for all Project order (POD) items, one item or you can use the multiselect function. Remember to start the process for getting assignments for all items, must be done on the Project order (POD) main level.
Select the Get material assignments for selected items option in the context menu. This means that the Project order (POD) item will get assignments from stock, procurement backlog, production work order or it will create a need for purchase or manufacturing.
In the Assignments status column you will e.g. see if the Project order (POD) item is in stock or if it must be purchased.
The status shown in this column is the status from the internal Sales order (COA) item that has been created for the purpose of getting assignments. In the Flow tab you can see which Sales order (COA) this Project order (POD) item is linked to.
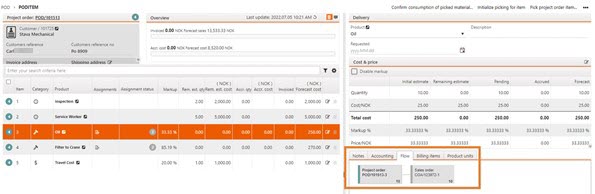
Get material assignments automatically during the Project order (POD) item registration
The process for getting assignments can be triggered automatically when a Project order (POD) item is registered. This is set with the Get material assignments automatically during project order item registration setting in the Company settings (CSV) application. If this setting is ON, the material assignments for a Project order (POD) item will be retrieved automatically during the registration.