Logistics process for a Project order (POD)
Material with assignment from stock can be picked according to the standard picking process. The process can be initialized for one Project order (POD) item at a time, or for all Project order (POD) items for material. When pick is initialized, it means that a pick can be confirmed via the Pick list (PICK) application on a computer or Confirm pick by handheld device (SCANPICK) on a handheld terminal (HHT). Therefore, the Project order (POD) item must have assignments from a Goods reception (SSA) item.
There will always be one common pick list for one Project order (POD), regardless of whether the pick is initiated by a Project order (POD) item, or from the Project order (POD) main level. Picklists created for a Project order (POD) will have the same name as the project order.
The picking process can also take place the opposite way. It may be that a user who needs a specific material only enters the warehouse defined in Location (LOC) in the Project order (POD), picks the material, scans the Goods reception (SSA) item or Product (ART) ID (#123456), Stock location (STL) and Project order (POD) ID. This can be done via the Pick (PODPICK) application on a Handheld Terminal (HHT).
If there is an internal Sales order (COA) item for this material in this Project order (POD), this will be confirmed as picked in RamBase. If there is no Sales order (COA) item, the system will create one and confirm specified quantity as picked. And if there is not an existing Project order (POD) item for this material, both Project order (POD) item and Sales order (COA) item will be created by the system and the specified quantity will be confirmed picked.
To allow picking by scanning the Product (ART) ID in Pick (PODPICK), these two settings must be turned on in the Company settings (CSV) application:
Allow to pick project order (POD) from another goods reception (SSA)
Allow to scan product id at pick of project order (POD)
Pick (PODPICK) can also be used to return material that has not been consumed to stock by use of the Unpick tab. This must be done before the material is confirmed as consumed.
Before material can be invoiced, it has to be confirmed as consumed. For a Fixed price Project order (POD), a dummy Sales invoice (CIN) will be created immediately when this confirmation is done.
Pick material for a Project order (POD)
It is only possible to pick material if the internal Sales order (COA) has assignments from stock.
These two Project order (POD) items defined in the image below have Status 8 which means that material is in stock and that it has assignments from Goods reception (SSA) item. If you enter the SAR icon, it will show which Goods reception (SSA) item. This is the standard process for RamBase and the same principle applies to Project orders (POD).

There are two steps for picking materials for a Project order (POD):
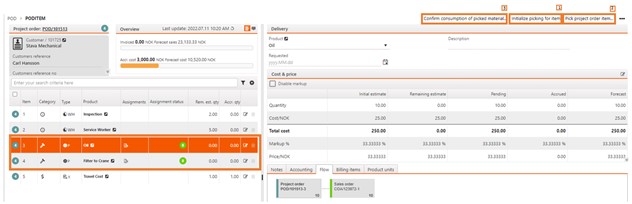
Step 1: Initialize picking
Step 2: Pick project order item. New image opens and standard picking process is performed.
To start the picking process a Project order (POD), you must first initialize picking for the items you want to pick.
You can choose between initializing picking for a single Project order (POD) item, all Project order (POD) items or use the multiselect function where you select several items initialize picking for. If you choose to use multiselect or want to pick all Project order (POD) items, this must be done from the main level on the Project order (POD).