Supplier Backlog Management (SBM)
The Supplier Backlog Management (SBM) application is an efficient tool for following up purchase orders. Typical examples may be when requested date deviates from confirmed date or if the confirmed date is overdue. The SBM could also be used to check status of unconfirmed supplier orders, and order items which are without any assignments to customer orders or production work orders. These cases often need immediate attention.
To open the Supplier Backlog Management (SBM) application, find Procurement in the RamBase menu and then Order handling. Click Purchase backlog management to enter the SBM application.
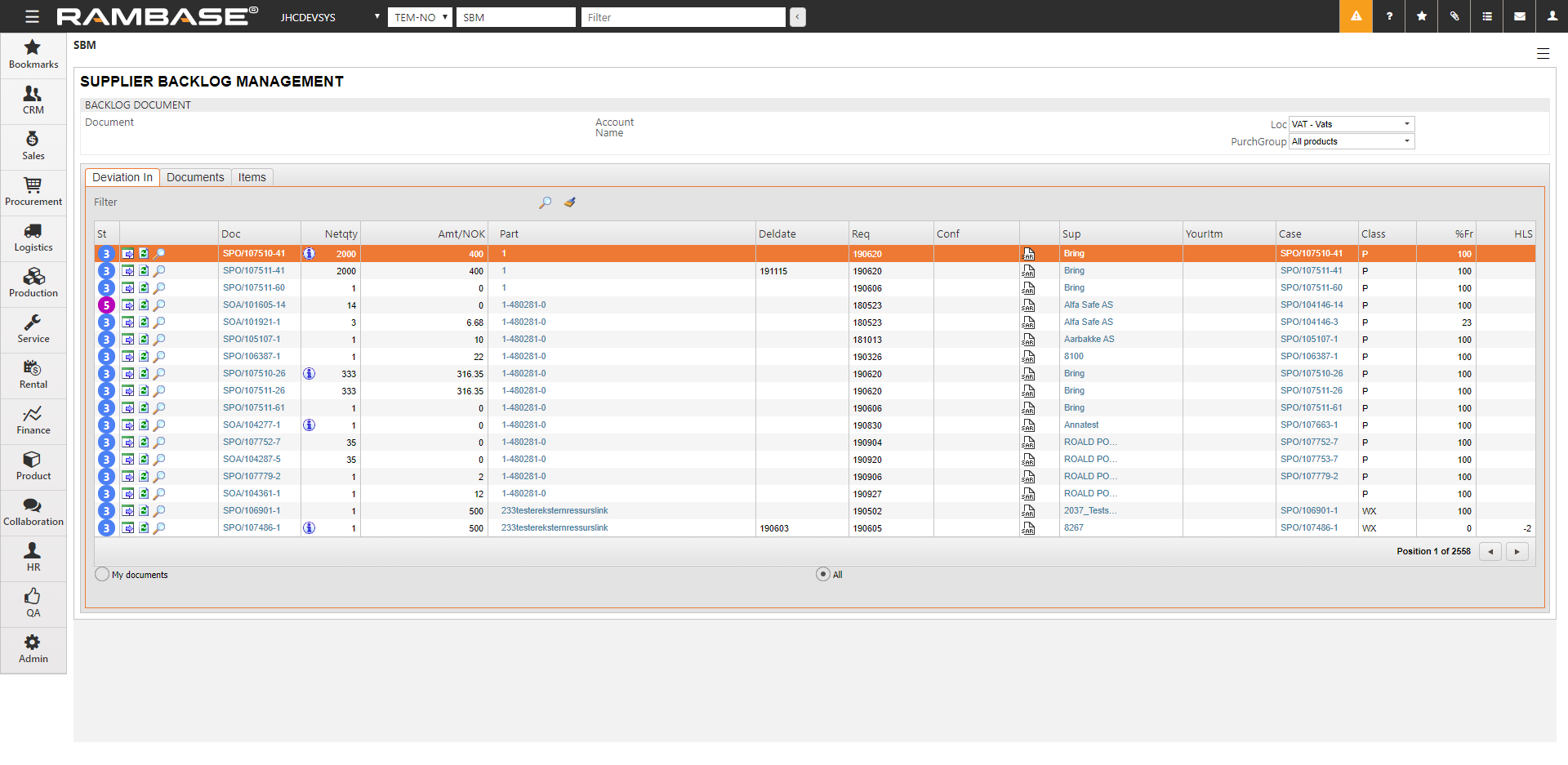
Field descriptions
Doc
Purchase Orders (SPO) and Purchase Order Responses (SOA).
NetQty
Remaining undelivered quantity on the specific order line.
Amount
Net Price * Quantity.
PART
Purchased part.
DelDate
Calculated delivery date for delivery to customer or production order. Delivery date is calculated by the system based on the requested/confirmed date, the customers delivery claims and available stock. If the customer accepts to receive delivery of goods before confirmed time when this is possible, the DelDate will be equal to Req date. If the Customer does not want to receive delivery of goods before confirmed time, the DelDate will be equal to Conf.
Req
The customers' requested delivery date.
Conf
The suppliers' confirmed delivery date.
YourItm
The Customers' order number.
Case
Reference to the original SPO.
C (Class)
Article classification code like P=Part, M=Material, K=Kit,...
Forecast
Sales forecast on article.
%Fr
(Percentage Free)Percent free of the requested item, means not allocated to customer or Production Work Orders (PWO).
HLSHigh/Low
Stock compared to the suppliers' confirmed delivery date. Calculated in number of days to late or to early delivery compared to required date from the customer or Production Work Order (PWO) the PO is allocated to.
You can filter the list by using the radio buttons at the bottom. This enables you to view all documents or only your documents, which is set as default.
The Supplier Backlog application enables you to have complete control over the supplier backlog. A supplier backlog may be defined as all purchase orders not yet received in stock. This overview may be defined with your own filters for personal customization.
Producing a file from the backlog
If you filter a selection of purchase orders, it is this selection which will be the basis for any reports sent to file. You may filter by article, supplier, date, amount and many others.
To produce a file from the backlog you press F12 to bring up the action menu and choose the option Download SBM to CSV file.
This will prompt a report job in RamBase and the file will be sent to the e-mail account registered to your PID.