LeadtimeCalculations (LTC)
The calculation method is designed to provide users with an estimated delivery date to the customer, taking into account the availability of goods. Users have the option to manually set a start date, which serves as the initial point for the calculation. The system will then estimate the earliest possible delivery date.
Header
The header provides details about the Sales order (COA) and the Product (ART) in question. The first section includes information on the product, description, revision, and available quantity.
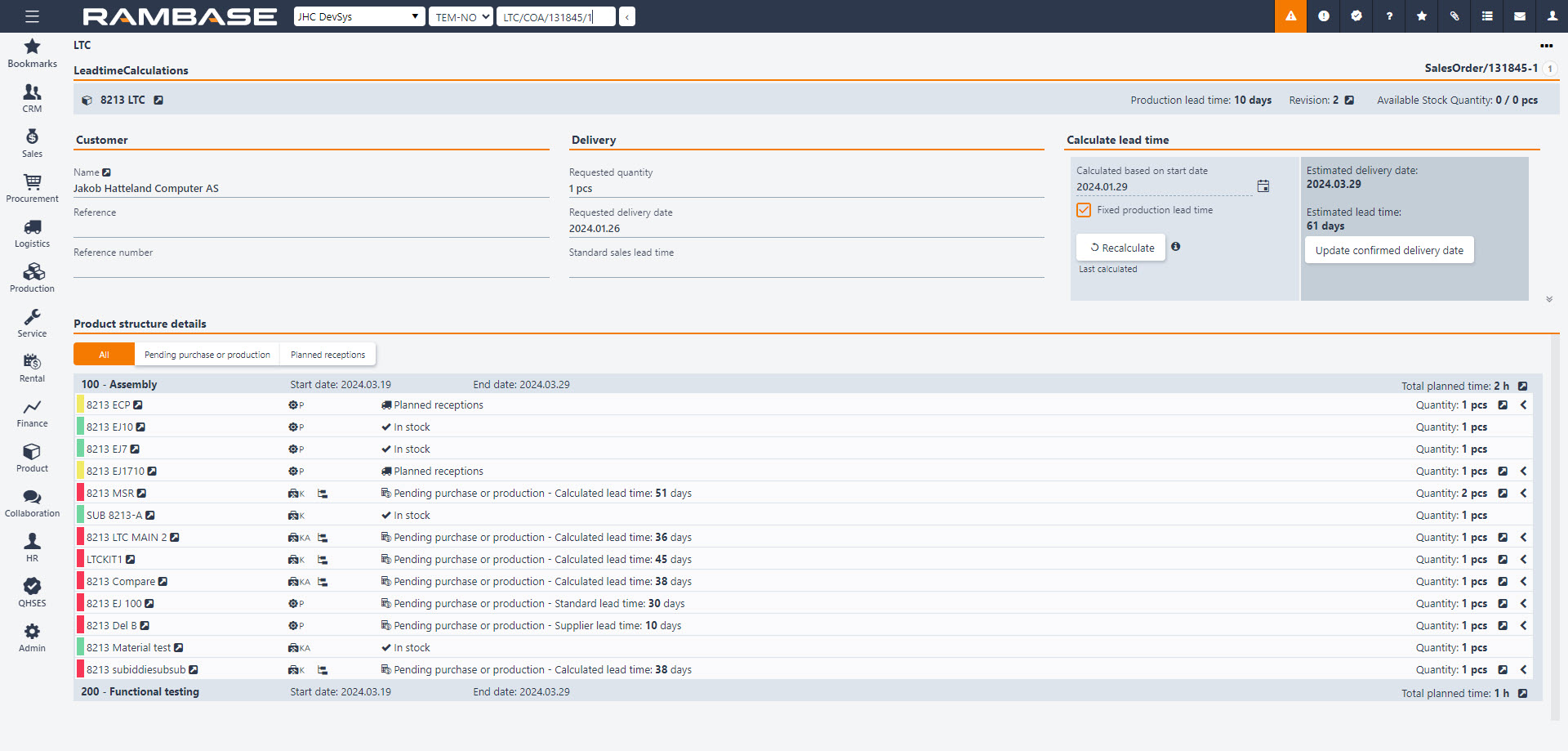
The section below contains sales order details, including customer information, references, and reference numbers. It also includes delivery specifics such as Requested quantity, Requested delivery date (derived from the sales order), and, if applicable, the Standard sales lead time for the sold product.
Columns | Description |
---|---|
Name | Customer name |
Reference | Customers reference |
Reference number | Customers reference number |
Requested quantity | Number of units ordered |
Requested delivery date | The delivery date as requested by the customer |
Standard sales lead time | The standard lead time, expressed in number of days, from when the customer places an order to delivery |
Calculated lead time area
The calculation method is designed to provide users with an estimated delivery date to the customer, taking into account the availability of goods. You have the option to manually set a start date, which serves as the initial point for the calculation. The system will then estimate earliest possible delivery date.
Columns/Fields/Buttons | Description |
---|---|
Calculated based on start date field | The initial starting point for the calculation |
Fixed production lead time checkbox | The predetermined number of days required to produce a given product |
Recalculate button | Recalculate the process |
Estimated delivery date | The estimated delivery date to the customer |
Estimated lead time | Total lead time presented in number of days |
Update confirmed delivery date button | Update the confirmed delivery date on a Sales order (COA) |
Fixed production lead time refers to the predetermined number of days required to produce a given product. When all components are available in stock, the fixed production lead time serves as a direct indicator of how quickly users can deliver the product. However, if users have dependent components that are currently out of stock and come with their own specified purchase lead times, one should add the number of days from the components purchase lead time to the fixed production lead time of the final manufactured product.
For example, if the fixed production lead time is 5 days and one component is not in stock with a purchase lead time of 7 days, the earliest possible delivery date would be 12 days from todays date.
Note
Note: Fixed production lead time should only be presented when the Company setting (CSV) Production planning based on production lead time is activated. Otherwise, this option should be hidden.
Note
The information in LeadTimeCalculations is a snapshot of the situation last time it was calculated for this object. If there have been changes in for example product structure, leadtimes, stock situation etc, use the Recalculate icon to update the information
Product structure details area
The KIT details section presents the product structure from the Product (ART) on the Sales order (COA), displaying all operations, components, and sub-assemblies.
Each operation is presented with its start and end date, along with the total planned time in hours. On mouseover, users also get presented the specific planned time to the corresponding processing times: Setup, Run time and Cleanup time. When inspecting one of the operations, it should direct you to the Production resource capacity and load overview (RCL) application with the filter set to the resource assigned to the operation.
There are three distinct statuses that a component or sub-assembly can have: In stock, Pending purchase or production, or Planned reception. These are also represented as filter options at the top on the KIT details section.
When the status is In stock, it signifies that the total required quantity is already available in the inventory, and no further action is necessary.
When the status is Pending purchase or production, it indicates that the required quantity is not currently in stock, necessitating an action such as procuring the component or initiating sub-assembly production.
When the status is Planned reception, it suggests that the required quantity is not in stock, but there is an active purchase order or ongoing production that will provide the necessary quantity to fulfill the requirement.
Sub-assemblies, which are products classified as KITs or KIT assemblies, can also be accessed and explored. When you navigate to one of these specified product types, you will be presented with the same overview for KIT details.