Line production method and setup
Planning method
The planning method for products where the Production Work Order (PWO) is designed to run at a production line with a continuous flow is different from the method used for ‘station based’ production. Running a production work order at a production line means that the planned start time of operation number 2 should be equal to the end time of the first product (unit) at operation number 1.
Overlapping operations:
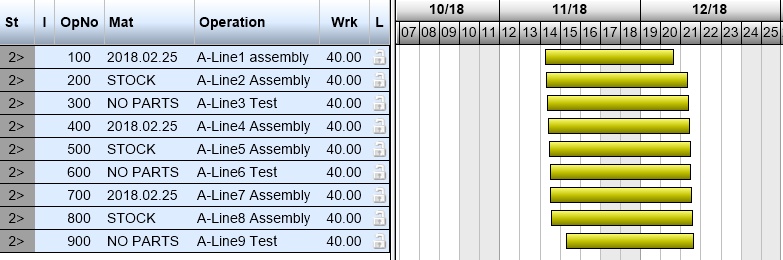
The total production time for the planned quantity will in this example be one week. If this product was set up with ‘station based’ planning the calculated total production time would be several weeks.
What is the impact / advantage of using line production planning
The line production method solves two issues:
The total production time for a PWO running on a line must be the time from the first product (unit) starts on the line till the last product leaves the line. This will give the correct load and period for the workload and capacity for the involved resources.
The material / parts requirement date is the start date of the operation that the material / parts are linked to. This has a direct influence on the required date for POs to supplier and the material/parts optimize processes. And these dates will not be correct when not using overlapping planning for a line production.
How to specify a product and product structure for line production
There are some criteria that must be followed to get the functions and planning method to run properly for a line production product:
All operations (OPR) must only have value in the ‘Time’ field (variable production time, production time per unit. They should never have ‘Pretime’ (setup time) or ‘Posttime’. That will not work, and the line is not flowing.
Queue time between operations must not be set, the process will not handle this. This is also a flow ‘blocker’.
How to enable line production method for a product
A product is either set for running at a production line or for ordinary ‘station based’ planning. There is no option to combine these methods for one product by letting some work orders run at the line and some at stations.
The line production method is enabled / disabled at the product (ART), ‘Misc’ folder, field ‘Lineproduction’ in the ‘DATA’ box. Value ‘Yes’ (1) = the product is set to be planned by the line production method.
Permission is given to the duty ‘Prepare product for production’.
Tools to support line production
The planning for a line production batch – both for resource planning and purchase planning – will most probably work best when the planning is done for one work order that holds the total quantity to be produced within a production period of 1-2 weeks (or other company preferences). A large order for a batch that needs several weeks of production time should probably be split into some smaller batches to get appropriate dates for purchase and planning.
A planned batch is also often preferred to be split into very small batches (some time down to 1 pcs per work order) when the production is to be started.
There is now available a new multi split tool that simplifies these split processes. The function is available at production work orders (PWO) that are registered but not released for production, that is: PWOs with status = 2, 3, 4.
F12 – Multisplit Permission given to duty: Plan production work orders
Multisplit preparation – building the split table
There are two methods to build the split table before confirming and starting the action.
Build split table by manually given units and dates:
The quantity and date is specified as shown in the red dotted box, and the line is added to the table below by the
sign.
Build split table by work orders and units:
Set number of work orders or number of units per order (the other number is calculated), the production start date and days between each start date:
The
builds the split table:
The suggested lines in the table can be deleted and the operations repeated until the table is as required.
Multisplit actions
There are two selectable actions (buttons) at the footer of the application (bottom of the screen):
Split and confirm
This function will split the PWO according to the specified table and confirm the new PWOs that are created. The new PWOs will get status = 2 or 3 or 4 when the split jobs are done.
Split and release
This function will split the PWO according to the specified table and both confirm and release all the PWOs (including the source) for production. All PWOs will get status = 5.
How is the split done?
The user will get a short notice on the screen when one of the actions is selected ‘Batch is started’ and the job is started. The involved PWOs are blocked for other actions while the batch job is running.
Please note that sub kits (sub PWOs) are not automatically split by the multisplit function even if the setting ProductionWorkOrderSplitSubOrder is set to ‘ON’. This is deactivated for line production products.