Sales and operation planning (SOP)
Sales and operations planning (SOP) is a planning tool that takes the sales forecast and creates a plan for production and purchasing to meet the sales requirements.
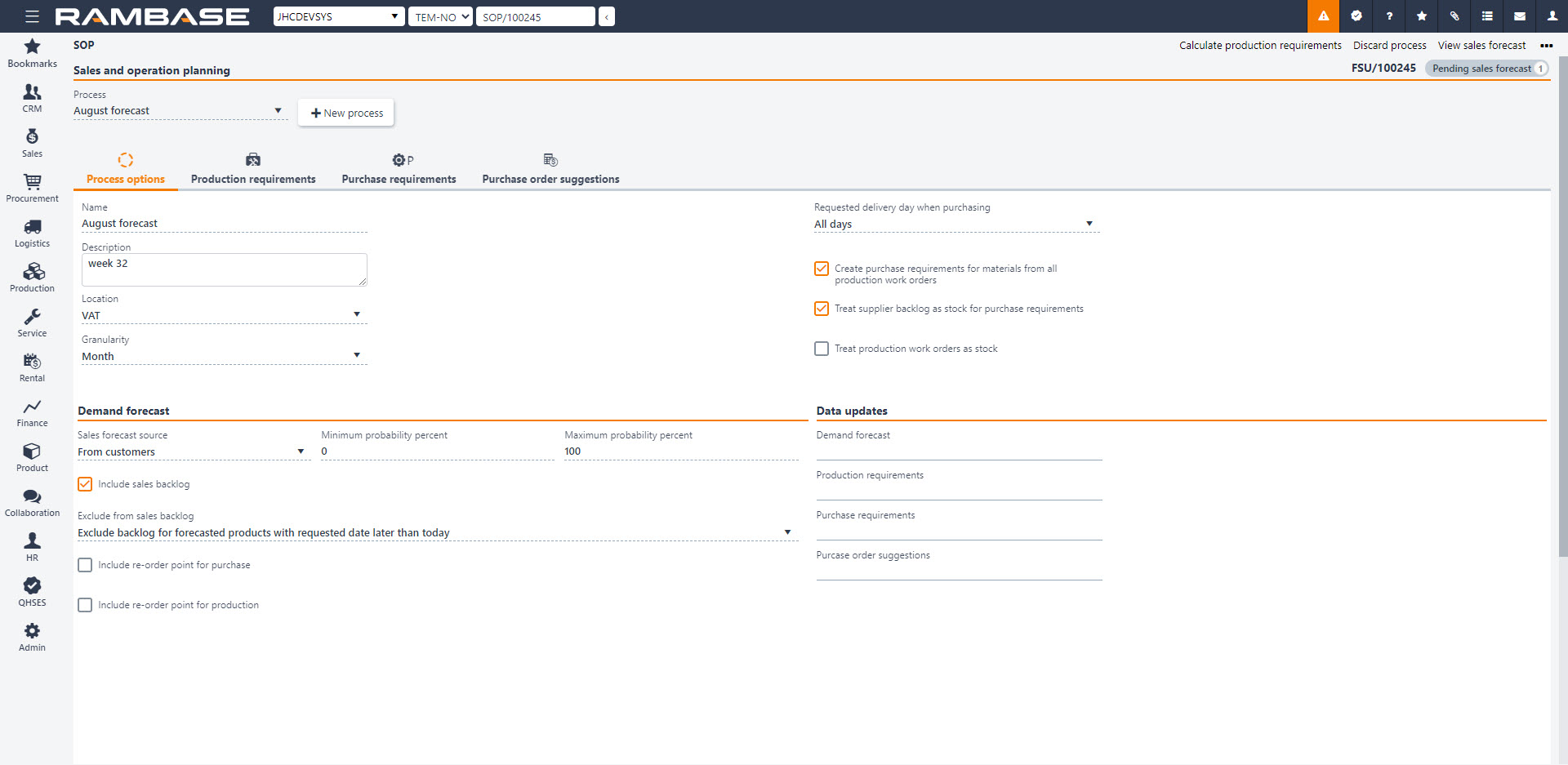
Description of the tab overview below:
Process options
This tab contains all information regarding the planning process.
General options:
Name field
Text field for entering a name for the process.
Description field
Text field for optional description.
Location drop-down menu
Location identifier
Granularity drop-down menu
Granularity used to present the different plans in the Sales operation planning process, either by week or month.
Requested delivery day when purchasing drop-down menu
Preferred day of delivery. Used to consolidate purchase order suggestions. Default is all days.
Create purchase requirements for materials from all production work orders checkbox
By enabling this option, materials from all ongoing and planned production work orders are included as gross purchase requirements. This means that you might get purchase requirements for materials belonging to production work orders not related to the production requirement plan. If this option is disabled, only materials needed to fulfill the production requirements are included as gross purchase requirements.
Note
Note that even if this option is disabled you will still get purchase requirements for materials in ongoing and planned production work orders (PWO) consumed by (net off) the production requirements.
Treat supplier backlog as stock for purchase requirements checkbox
By enabling this all purchase orders and purchase order responses will be treated as stock. Any purchase orders and purchase order responses confirmed in the future (ex. in two months) is available from today and can be used to net off purchase requirements. By not enabling this, you might end up with purchasing products that could instead be acquired by requesting change of delivery date on existing supplier backlog.
Treat production work orders as stock checkbox
By enabling this, existing, but not completed, production work orders will be treated as stock. Any production work orders can be used to net off production requirements. By not enabling this, you might end up with creating new production work orders instead off re-planning already existing production work orders.
Demand forecast area
Sales forecast source drop-down menu The source to use from the sales forecast.
Include sales backlog checkbox
If sales backlog is included, everything from the backlog is added to the demand forecast. Note that backlog from products sales forecast by customers (through the sales forecast source), will not be included.
Minimum and maximum probability percent field
Minimum and maximum probability in percentage to include from the sales forecast
Include re-order point for purchase checkbox
If products which are purchased have specified re-order point quantity for the location used in the Sales and operation planning process, the re-order point quantity will be added as a demand. This will then be included in the gross quantity of the purchase requirements. Note that this also includes products with product structures manufactured externally.
Include re-order point for production checkbox
If products which are manufactured have specified re-order point quantity for the location used in the Sales and operation planning process, the re-order point quantity will be added as a demand. This will then be included in the gross quantity of the production requirements. Note that this does not includes products with product structures manufactured externally.
Demand forecast
Date and time demand forecasts were created
Production requirements
Date and time production requirements were updated for this Sales and operation planning process.
Purchase requirements
Date and time purchase requirements was updated in this Sales and operation planning process.
Purchase order suggestions
Date and time purchase requirements was updated in this Sales and operation planning process.
Production requirements
This tab shows all production requirements which follows the sales forecast. Each production requirement represents a product and a requested delivery date.
Key fields are:
Updated at
Date and time production requirements were updated.
Requested delivery date
The delivery date as requested.
Product
The required product
Available quantity
Total quantity available to be subtracted from the demand quantity (gross quantity). This is the sum of all goods receptions and production work orders ready to be consumed at requested delivery date.
Gross quantity
Gross quantity of the production requirement. This is the total demand before any subtractions or adjustments is considered. Initially set as the sales forecast quantity, but will be changed if the net quantity of parent product structures changes.
Adjusted quantity
Quantity adjusted by the users. Can be both negative and positive. The sum of gross quantity and adjusted quantity can never be less than zero.
Subtracted quantity
Quantity of stock and production work orders subtracted from the gross quantity.
Production adjusted quantity
Some products are only produced in multiple of a specified quantity. In that case, the net quantity might need an adjustment.
Net quantity
Net production requirement quantity. This is calculated by subtracting production work orders, stock and adjusted quantity from the gross quantity.
Treat production work orders as stock
By enabling this, existing, but not completed, production work orders (PWO) will be treated as stock. Any production work orders can be used to net off production requirements. By not enabling this, you might end up with creating new production work orders instead off re-planning already existing production work orders.
Purchase requirements
This tab shows all the purchases required to fill the orders. Each purchase requirement represents a product and a requested delivery date.
Options related to purchase requirements:
Treat supplier backlog as stock
By enabling this all purchase orders and purchase order responses will be treated as stock. Any purchase orders and purchase order responses confirmed in the future (ex. in two months) is available from today and can be used to net off purchase requirements. By not enabling this, you might end up with purchasing products that could instead be acquired by requesting change of delivery date on existing supplier backlog.
Require materials from all production work orders
By enabling this option, materials from ALL ongoing- and planned production work orders are included as gross purchase requirements. This means that you might get purchase requirements for materials belonging to production work orders not related to the production requirement plan. If this option is disabled, only materials needed to fulfill the production requirements are included as gross purchase requirements. Note that even if this option disabled you will still get purchase requirements for materials in ongoing- and planned production work orders consumed by (net off) the production requirements.
Key fields are:
Updated at
Date and time purchase requirements were updated
Requested delivery date
The delivery date as requested by the customer.
Product
The required product.
Available quantity
Total quantity available to be subtracted from the gross quantity. This is the sum of all goods receptions, purchase orders and purchase order responses ready to be consumed at requested delivery date.
Gross quantity
Gross quantity is initially the same as the sales forecast quantity but might have changed during the production requirement planning. The gross quantity is the final required quantity for given product at requested delivery date.
Subtracted quantity
Quantity of stock, purchase orders and purchase order responses subtracted from the gross quantity.
Net quantity:
Net purchase requirement. This is the quantity needed to be ordered for this product at this requested delivery date. The net quantity is calculated by subtracting stock, purchase orders and purchase order responses from the gross quantity.
Purchase order suggestions
This tab creates purchase orders for all the purchase requirements, based on the information from the Sales and operation planning (SOP). Each purchase order suggestion represents a product and a requested delivery date.
Options related to purchase order suggestions:
Requested delivery day
Preferred day of delivery. Used to consolidate purchase order suggestions. Default is all days.
Each purchase order suggestion represents a product and a requested delivery date.
Key fields are:
Updated at
Date and time purchase order suggestions were updated.
Requested delivery date
The delivery date as requested.
Product
The required product.
Supplier
The suggested supplier.
Suppliers product name
Suppliers product name.
Lead time
Lead time for product and suggested supplier.
Deadline date
Deadline for purchasing product from supplier. Calculated by subtracting lead time from requested delivery date.
Quantity
Quantity suggested to purchase.
Gross purchase price
Gross price of the purchase order suggestion.
Gross requirement quantity
The gross demand for supplier, product and requested delivery date.
Subtracted requirement quantity
Quantity from open purchase orders and purchase order responses subtracted from the gross demand quantity to get the net demand quantity.
Net requirement quantity
Net demand quantity for this product, supplier and requested delivery date. The net quantity is the current demand, and will be the base for creating the quantity of the purchase order suggestion.