Metoda linii produkcyjnej i konfiguracja
Metoda planowania
Metoda planowania dla produktów, w których zlecenie produkcyjne (PWO) jest zaprojektowane dla linii produkcyjnej z ciągłym przepływem różni się od metody używanej dla produkcji na „stacjach”. Uruchamianie zlecenia produkcyjnego na linii produkcyjnej oznacza, że zaplanowany czas rozpoczęcia operacji numer 2 powinien być równy czasowi zakończenia pierwszego produktu (jednostki) w operacji numer 1.
Nakładające się operacje:
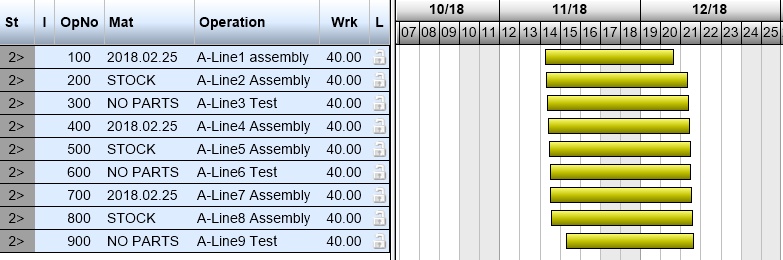
Całkowity czas produkcji dla planowanej ilości będzie w tym przykładzie wynosił jeden tydzień. Jeśli produkt został utworzony za pomocą planowania dla produkcji na „stacjach”, obliczony całkowity czas produkcji będzie wynosił kilka tygodni.
Wpływ/zaleta korzystania z planowania dla linii produkcyjnej
Metoda linii produkcyjnej rozwiązuje dwa problemy:
Całkowity czas produkcji dla PWO uruchamianego na linii produkcyjnej musi być czasem z rozpoczęcia produkcji pierwszego produktu (jednostki) na linii do momentu opuszczenia linii przez ostatni produkt. Zapewni to prawidłowe obciążenie i okres dla nakładu pracy i zdolności produkcyjnej dla zaangażowanych zasobów.
Data wymagania materiału/części jest datą rozpoczęcia operacji, z którą materiał/części są połączone. Ma to bezpośredni wpływ na wymaganą datę dla PO dla dostawcy oraz procesy optymalizacji materiałów/części. Te daty nie będą prawidłowe, jeśli dla linii produkcyjnej nie zostanie użyte nakładające się planowanie.
Określanie produktu i struktury produktu dla linii produkcyjnej
Istnieją pewne kryteria, które muszą być przestrzegane, aby móc korzystać z funkcji i metody planowania do prawidłowego uruchamiania liniowej produkcji produktu.
Wszystkie operacje (OPR) muszą mieć wartość tylko w polu „Czas” (zmienny czas produkcji, czas produkcji na jednostkę). Nigdy nie powinny mieć wartości „CzasPrzed” (czas konfiguracji) i „CzasPo”. W przeciwnym wypadku produkcja na linii produkcyjnej nie będzie się odbywać.
Czas kolejki pomiędzy operacjami nie może być skonfigurowany, ponieważ proces go nie przetworzy. Jest to również „blokada” przepływu.
Włączanie metody linii produkcyjnej dla produktu
Produkt jest skonfigurowany do uruchamiania linii produkcyjnej lub dla zwykłego planowania produkcji na „stacjach”. Nie ma możliwości łączenia tych metod dla jednego produktu, aby niektóre zlecenia uruchamiały produkcję na linii a inne na stacjach.
Metodę linii produkcyjnej włącza/wylącza się w produkcie (ART), folderze „Różne”, polu „LiniaProdukcyjna” w polu „DANE”. Wartość „Tak” (1) = produkt jest skonfigurowany na planowanie według metody linii produkcyjnej.
Uprawnienie jest przyznane obowiązkowi „Przygotuj produkt do produkcji”.
Narzędzia do obsługi linii produkcyjnej
Planowanie dla serii linii produkcyjnej, dla planowania zasobów i planowania zakupu, będzie działać najlepiej, gdy planowanie odbywa się dla jednego zlecenia, które zawiera całą ilość do wyprodukowania w obrębie okresu produkcji wynoszącym 1–2 tygodnie (lub innym, według preferencji firmy). Duże zamówienie na serię, której wyprodukowanie wymaga kilku tygodniu, najlepiej podzielić na mniejsze serie, aby móc oszacować daty dla zakupu i planowania.
Planowaną serię często dzieli się na bardzo małe serie (niektóre nawet na 1 szt. na zamówienie), gdy produkcja ma zostać uruchomiona.
Obecnie dostępne jest nowe narzędzie do podziału wielokrotnego, które upraszcza te procesy podziału. Funkcja jest dostępna w zleceniach produkcyjnych (PWO), które są zarejestrowane, ale nie są zwolnione dla produkcji, czyli: PWO ze statusem o wartościach = 2, 3, 4.
F12 – Podział wielokrotny Uprawnienie przyznane obowiązkowi: Planowanie zleceń produkcyjnych
Przygotowanie podziału wielokrotnego – tworzenie tabeli podziału
Istnieją dwie metody tworzenia tabeli podziału przed potwierdzeniem i rozpoczęciem akcji.
Tworzenie tabeli podziału według ręcznie podanych jednostek i dat:
Ilość i data są określone w sposób podany w czerwonym kropkowanym polu, a wiersz dodaje się do poniższej tabeli za pomocą znaku
.
Budowanie tabeli podziału według zleceń i jednostek:
Skonfiguruj liczbę zamówień lub liczbę jednostek na zamówienie (inna liczba jest obliczana), datę rozpoczęcia produkcji i dni pomiędzy każdą datą rozpoczęcia:
.
tworzy tabelę podziału:
Sugerowane wiersze w tabeli mogą zostać usunięte, a operacje powtarzane do momentu, gdy tabela będzie wymagana.
Akcje podziału wielokrotnego
W stopce aplikacji (dół ekranu) dostępne są dwie wybieralne akcje (przyciski):
Podziel i potwierdź
Ta funkcja podzieli PWO zgodnie z określoną tabelą i potwierdzi nowe PWO, które zostaną utworzone. Nowe PWO otrzymają status o wartości = 2, 3 lub 4, gdy zadania podziału zostaną wykonane.
Podziel i zwolnij
Ta funkcja podzieli PWO zgodnie z określoną tabelą i potwierdzi oraz zwolni wszystkie PWO (w tym źródłowe) dla produkcji. Wszystkie PWO otrzymają status o wartości = 5.
Jak odbywa się podział?
Na ekranie użytkownika pojawi się krótkie powiadomienie „Seria jest rozpoczęta”, gdy jedna z akcji zostanie wybrana i zadanie zostanie uruchomione. Uwzględnione PWO są blokowane dla innych akcji, a zadanie wsadowe jest uruchamiane.
Pamiętaj, że zestawy podrzędne (podrzędne PWO) nie są automatycznie dzielone przez funkcję podziału wielokrotnego, nawet jeśli ustawienie DzielZamówieniaPodrzędneZleceniaProdukcyjnego ma wartość „WŁ.”. Ustawienie jest dezaktywowane dla produktów linii produkcyjnej.