[en] Material requirements planning
[en] Material requirements planning applications, requirements plan- and overview, is used to calculate the materials and components of manufactured products, and provide you with information on what must be available, in right quantities- and time.
[en] The material requirements planning applications aims to show, how various transactions affect both physical- and available stock, identify deviations and provide you with purchase- and Production work order (PWO) suggestions.
[en] Requirements plan
[en] The requirements plan is presented in the context of an item, and can have several inputs. These are:
[en] Demands originating from Sales orders (COA) and/or Sales forecasts (FCC). How much is wanted and when is it wanted - considered as independent demand.
[en] On-hand stock quantities and inventory management data.
[en] Bill of materials (BOM) - what and how much is required of sub-assemblies, components and material - considered as the dependent demand.
[en] Products (ART) application item will have an overview by clicking Stock and then the Requirements plan tab. The overview can be used for both production- and purchase planning purposes, but also during sales. The intention is to create a more structured planning process, as well as making it more efficient to check for availability of products, materials and components.
[en] The presented transactions in the overview is based on actual linking in the background Stock assignment (SAR). There will be a nightly batch that calculates the requirements, but also with an option of manually triggering it when desired.
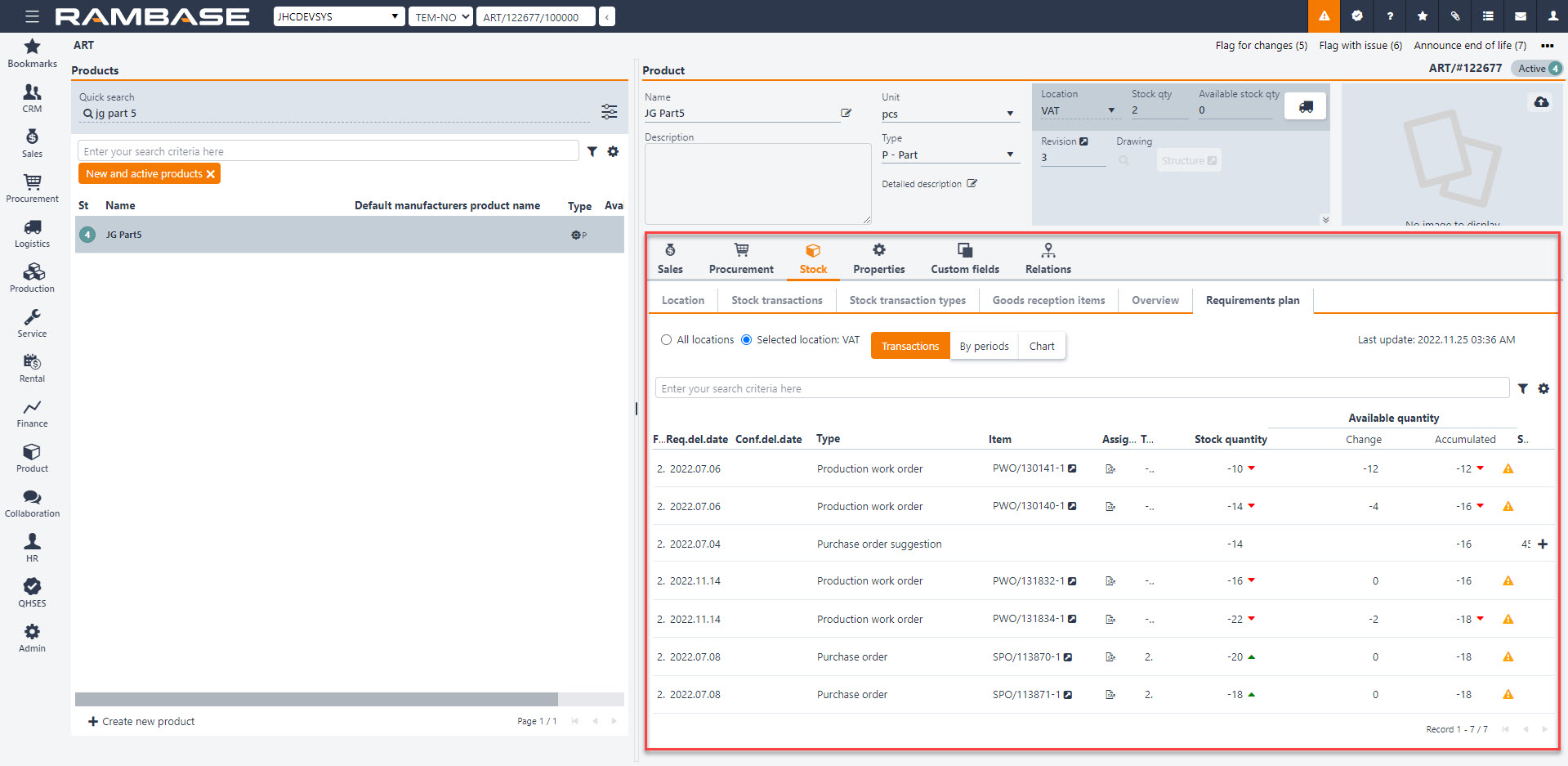
[en] Transactions
[en] The requirements plan is presented per item. General information such as stock quantity, available quantity and location for the item in question, is displayed in the item header.
[en] The transaction overview presents each transaction with planned date and related quantity, planned accumulated stock with reference to the source document and reference information depending on actual transaction – Purchase orders (SPO), Sales orders (COA), or Production work orders (PWO). The list is sorted on date, and it is also possible to present it per different periods. When sorting the list on period, the transactions are consolidated.
[en] Transactions such as Sales orders (COA), Production work orders (PWO) (if it is a component, material, or sub-assembly in another manufactured product) and sales forecast are examples on what could decrease the stock. Whereas Purchase orders (SPO) and Production work orders (PWO) are two examples on what increases stock.
[en] When registering an order on a manufactured product, the requirements plan should show the initial requirement on top-level (sold product), as well as requirements for all components and materials included in the product bill of material. The sold product should have a reference to the Sales order (COA), whereas the components and materials should have a reference to the Production work order (PWO) if it is created. If the Production work order (PWO) is not created for the sold product, then the requirements plan for the underlying components, assemblies etc. will have a reference to the product it is withdrawn to.
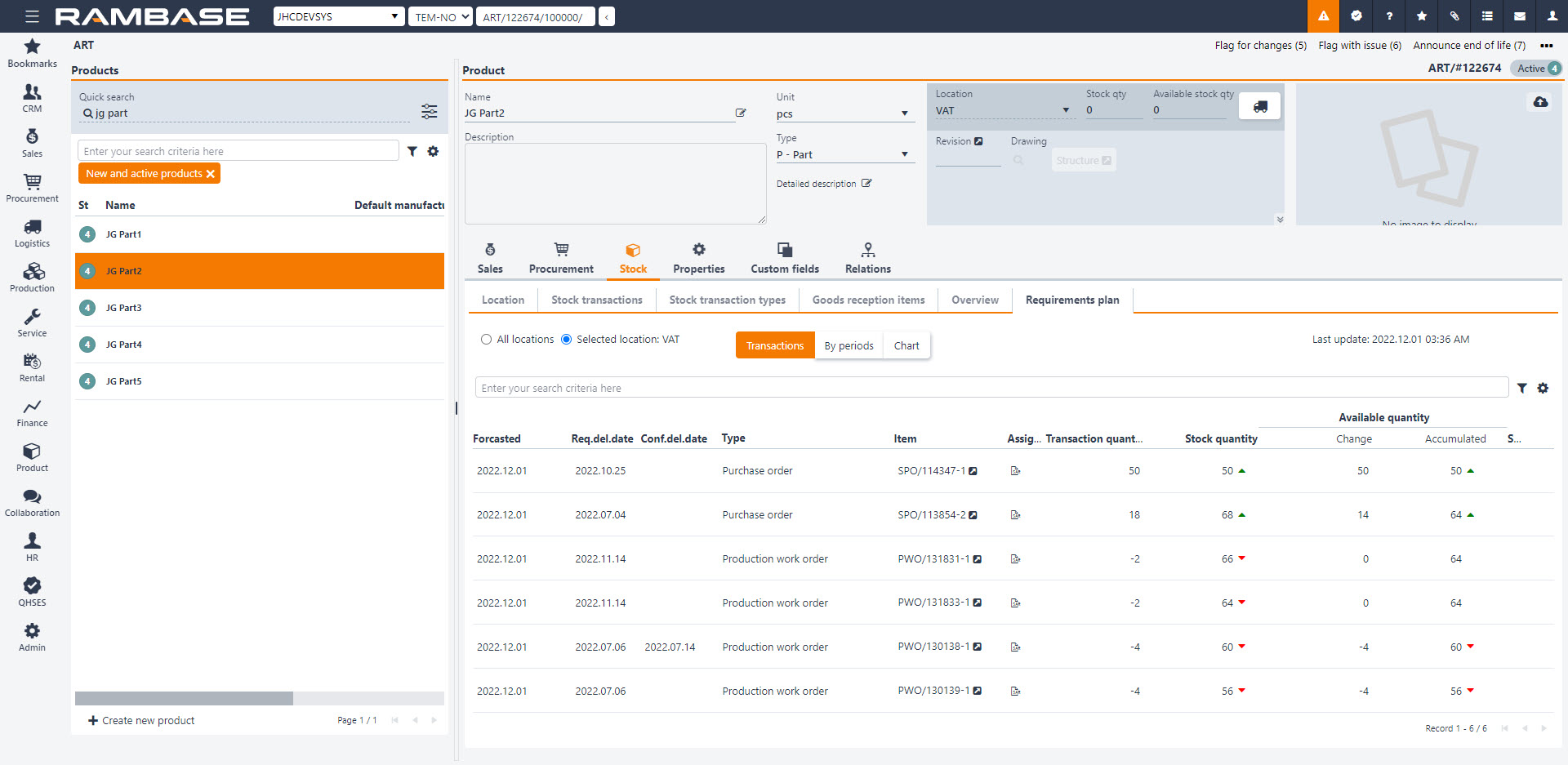
[en] From the presented requirements plan you are able to see that the first two lines are purchase orders that increase stock for the item in question, but also how the next production work orders decrease stock. This is how you should be able to follow the material requirements plan on all the different items and see how it will affect the inventory of this particular item. The clue here is to be able to easily identify the instances where deviations occur.
[en] Column name | [en] Description |
---|---|
[en] Estimated date | [en] Sorting based on date. Required or confirmed date is used if the defined date is not in the past. If the date is in the past, todays date is used. |
[en] Req.del.date | [en] Requested delivery date. |
[en] Conf.del.date | [en] Confirmed delivery date. |
[en] Type | [en] Type of product. |
[en] Item | [en] Name of the document and item numbers are displayed. |
[en] Assignments | [en] Stock assignment register. |
[en] Transaction quantity | [en] Quantity related to the transaction in question. |
[en] Stock quantity | [en] Physical on hand quantity. Includes allocated items. |
[en] Available quantity | [en] On hand quantity that is not allocated. Displays changes (increase and decrease) in available quantity. |
[en] Suggested | [en] Suggested purchase- or production quantity. |
[en] In summary, it is a material plan that shows how the various transactions affect both physical- and available stock.
[en] By periods
[en] Column name | [en] Description |
---|---|
[en] Period/Type | [en] Transactions collected at either weekly level, monthly level, quarter or year. |
[en] Available in stock | [en] On hand quantity that is not allocated. |
[en] Suggested quantity | [en] Total suggested purchase- or production quantity for the defined period. |
[en] Stock quantity | [en] Physical on hand quantity. Includes allocated items. |
[en] Increase in stock | [en] Total increase in stock quantity for the defined period. |
[en] Decrease in stock | [en] Total decrease in stock quantity for the defined period. |
[en] Change in quantity | [en] Total change in stock quantity for the defined period. |
[en] In addition there are different ways of grouping, called By periods. If we compare By period and Transactions, by period is a grouping of the various periods, this controls how you want to plan.
[en] Chart
[en] Chart illustrates development of stock over time, where parameters such as re-order point, available stock, stock quantity and 0-level are presented.
[en] Column name | [en] Description |
---|---|
[en] Stock quantity | [en] Development of physical stock. Includes allocated items. |
[en] Available quantity | [en] Development of available stock. |
[en] 0-level | [en] 0-level. |
[en] Reorder point | [en] The level of inventory which triggers an action to replenish that particular inventory stock. |
[en] Reorder point
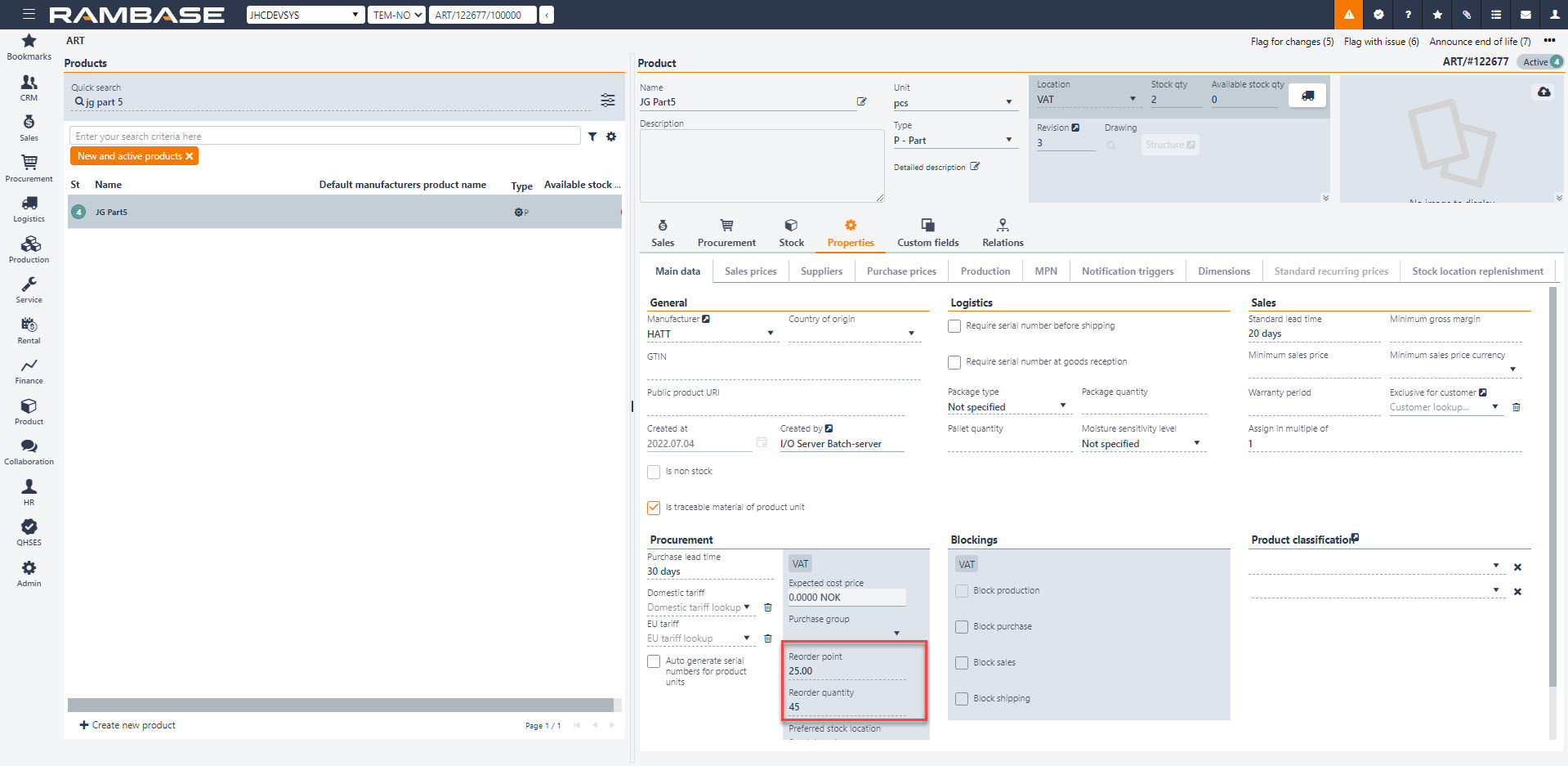
[en] The reorder point is the level of inventory which triggers an action to replenish that particular inventory stock. When the defined re-order point is reached, it will trigger either a purchase- or production need, depending on what type of item it is. In this image there is a reorder point of 25.
[en] Purchase- and Production work order (PWO) suggestions will also be displayed in the requirements plan. When a deviation occurs, negative available stock or below re-order point, a suggestion will be presented. The suggested quantities will consider parameters from the item, such as: re-order quantity, suppliers minimum order quantity and package quantity on bought items, and minimum production order quantity and multiple quantities on manufactured items. The suggested quantity can also be adjusted for the manufactured items.
[en] Requirements overview (REO) application
[en] The requirements overview (REO) application consists of two tabs, purchase order- and production work order suggestions. These tabs represent all items with deviation, e.g. negative available stock or available stock below reorder point, from the requirements plan. The purpose is to have one common overview where all items with deviation are identified and where all necessary actions can be taken.
[en] All details behind the presented figures can be inspected. This will lead you to the requirements plan for the item in question. Additionally, both purchase- and Production work orders (PWO) can be created directly from the overview. By doing so, you will create Purchase orders (SPO) or Production work orders (PWO) in Status 1.
[en] There are several filter options presented for both tabs. These are: location (option for both tabs) supplier and purchase group for purchase order suggestions, and manufacturing area and planning category for production work order suggestions.
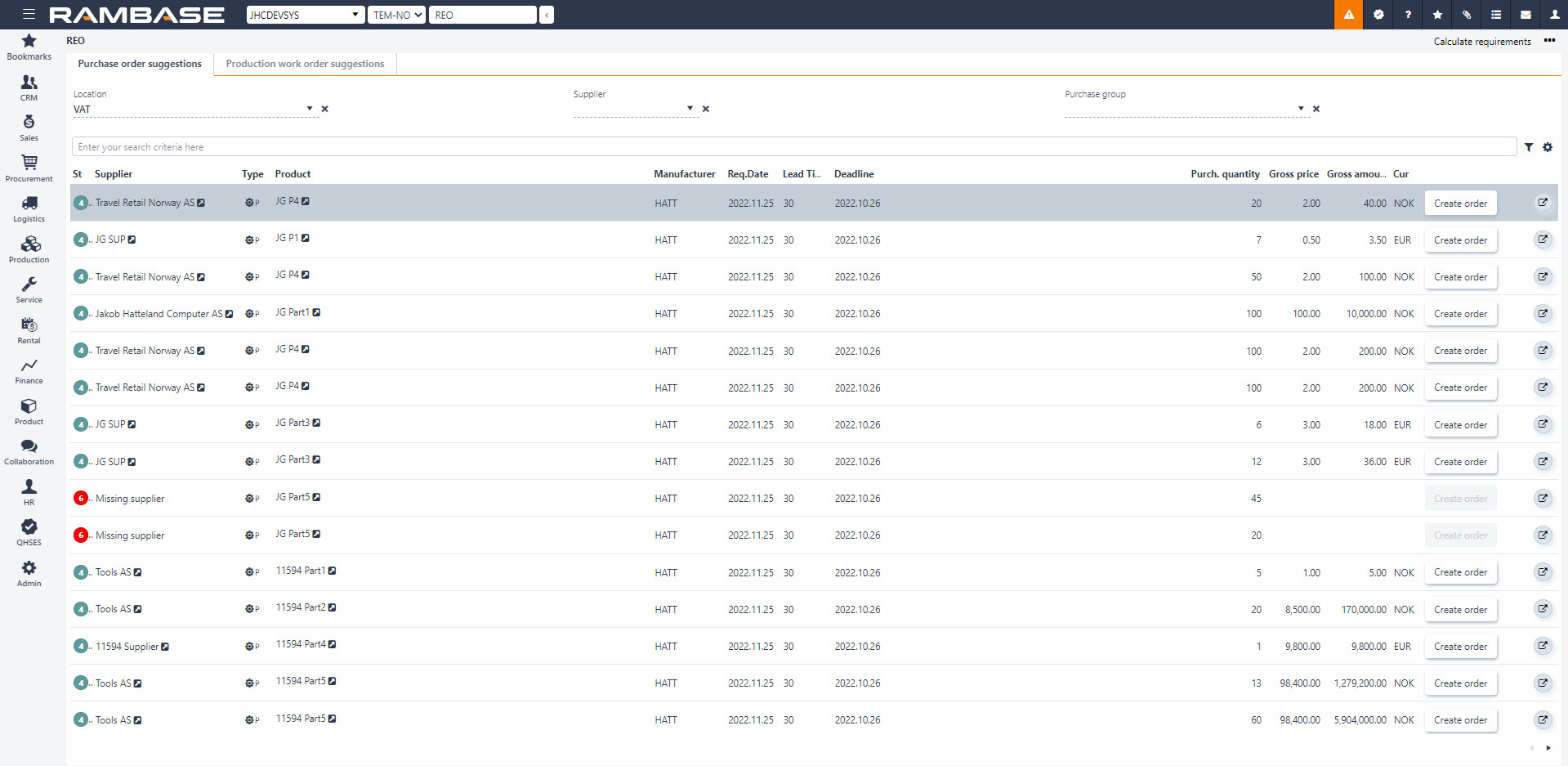